Maddock mixers are popular and effective mixers for single-screw extruders (and injection molding plasticators) because of their low cost to build and their ability to provide a uniform level of dispersive mixing. If the mixer is designed properly, all entering solid polymer fragments and certain types of polyethylene (PE) gels can be trapped and dispersed into the matrix resin.
Many Maddock mixers that are used commercially, however, provide lower levels of dispersive stress mixing than required by the process. Moreover, a poorly designed mixer can cause resin to degrade. The degraded resin will eventually contaminate the product, especially film products where degradation defects are easy to see.
Maddock mixers are popular and effective mixers for single-screw extruders (and injection molding plasticators) because of their low cost to build and their ability to provide a uniform level of dispersive mixing. If the mixer is designed properly, all entering solid polymer fragments and certain types of polyethylene (PE) gels can be trapped and dispersed into the matrix resin.
Many Maddock mixers that are used commercially, however, provide lower levels of dispersive stress mixing than required by the process. Moreover, a poorly designed mixer can cause resin to degrade. The degraded resin will eventually contaminate the product, especially film products where degradation defects are easy to see.
A common feature for single-screw extruder screws for plasticating amorphous and semicrystalline resin is the positioning of a mixer near the end of the screw. For many applications, the mixer should be a dispersive type such that solid polymer fragments are trapped, melted and dispersed before discharging to the downstream equipment. There are numerous mixers that can be used, but a Maddock mixer is preferred for many applications.
The most common screw design for producing PE film and sheet utilizes a barrier melting section followed by a Maddock mixer. The mixer traps and melts a low level of solid polymer fragments exiting from the solids channel of the barrier melting section. The mixer is typically positioned in the metering section about 2 diameters from the discharge. When designed properly, this combination has proven success with plasticating many resins, including PE resins at high rates and low discharge temperatures required for blown film applications.
A poorly designed mixer can cause resin to degrade.
The first fluted mixer patent was issued to Gene Leroy of the Union Carbide Corp. (UCC) in 1969 for the controlled degradation of thermoplastic materials rather than as a dispersive mixer. Bruce Maddock realized the device had potential as a dispersive mixer and commercialized it for single-screw extruders. The device is known as the Maddock mixer, Leroy mixer or the UCC mixer. The mixer had such a large impact on improving the melt quality for PE blown film applications that UCC released its patent rights to the public domain.
The device is constructed by cutting several pairs of fluted channels into the screw in the axial direction, as shown in Figure 1. Each pair is designed with an in-flow flute and an out-flow flute. Between these flutes is a mixing flight that is undercut from the main flight. All resin must flow through the gap between the mixing flight and the barrel wall. The mixing flight traps any solid polymer fragments and disperses them into the molten resin matrix. The number of flute pairs depends on the diameter of the screw. The mixer length is typically about 2 diameters. Many variations have been developed and patented over the years, including the spiral Maddock mixer where the flutes typically have a 60-degree helix angle.
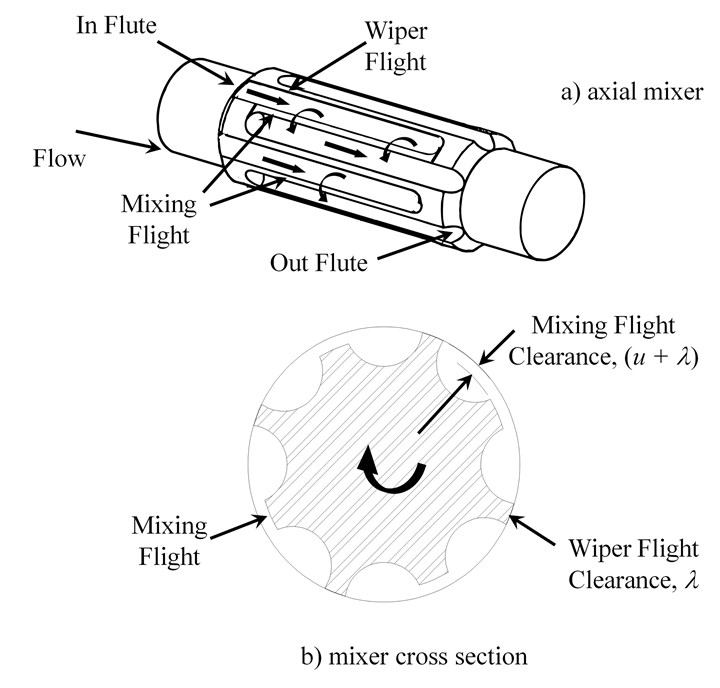
FIG 1 Schematic of a Maddock mixer with axial flights. Images: M. Spalding
A common gel type for PE resins is an unmixed or entangled gel. When these gels discharge from a film die, they are clear and usually cannot be detected. But because they are entangled, they typically solidify and crystallize differently from the bulk of the film. They often appear as unmelted material with diameters of 0.5 to 1.0 mm. When these gels are examined using a hot-stage microscope, they melt at the same temperature as the matrix of the film, and they reform when cooled. Photographs of the process are shown in Figure 2.
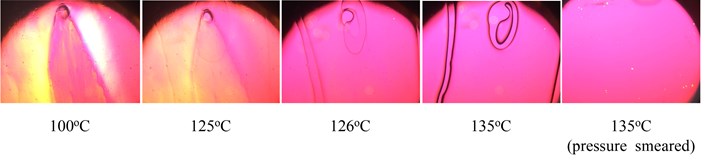
FIG 2 Photographs of an entangled gel at select temperatures using a hot-stage microscope. The circular segment of the gel in the photograph at 100oC had a diameter of about 0.8 mm. As shown by this sequence of photographs, the gel melted at about 135oC. When the gel was smeared by moving the glass cover plate, the stress was enough to disentangle the polymer chains such that the gel would not reappear upon cooling.
The gel sample is typically placed on a glass slide with a drop of silicone oil and covered with a thin glass cover plate. When the sample is heated to about its melting temperature and the gel is stressed by pushing on the glass cover slip with a dental tool, the gel is disentangled. Now when the sample is cooled, the gel does not reform. That is, the applied stress has untangled the chains, enabling it to have an identical morphology as the rest of the film and thus it is no longer visible.
Avoid Too Many Flute Pairs
The number of flute pairs and the shape of the flutes are very important design parameters. A common design error is to use too many flute pairs. Designs with too many flute pairs will force the designer to make the flutes very deep and narrow. The deep flutes can often lead to the degradation of the resin, as shown in Figure 3. In this figure, brown degraded PE resin is visible at the pushing and trailing edges of flutes. Here, the flutes were designed too deep to mitigate pressure consumption through the mixer because too many flute pairs were used.
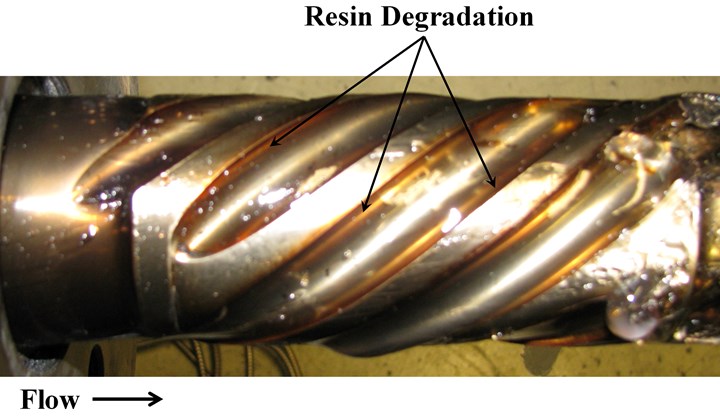
FIG 3 Photograph of a Maddock mixer with flutes that are too deep, causing resin degradation at the pushing and trailing sides of the flutes.
The flutes are typically cut into the screw using ball end mills. The width of the flute is set by the diameter of the milling tool. The optimal flute shape perpendicular to the edge is a semicircle which is created by milling into the steel such that the deepest part of the flute is half the flute width. These flow paths are shown on poorly designed flutes and effective flutes in Figure 4. As shown in Figures 4a and 4b, the flutes were cut too deep, while the flutes shown by Figures 4c and 4d are effective with the flute depth at half of the width.
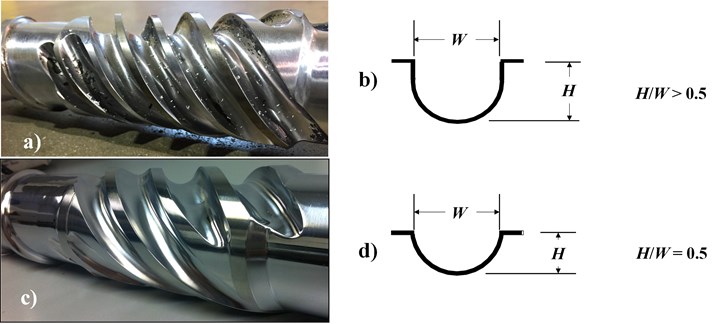
FIG 4 Effective and poor Maddock mixer designs: (a) a photograph of a poor design with very deep flutes, (b) a schematic of a deep flute (poor design) where the depth is greater than half of the width, (c) photograph of an effective design with well-designed flutes and (d) a schematic of an effectively designed flute where the depth is equal to half of the width.
Optimal flute configurations are provided in the accompanying as a function of barrel diameter. As presented earlier, the number of flute pairs increases with barrel diameter. The width of the flights perpendicular to the flute edges is calculated by evenly spacing the flutes on the circumference of the outside diameter of the screw.
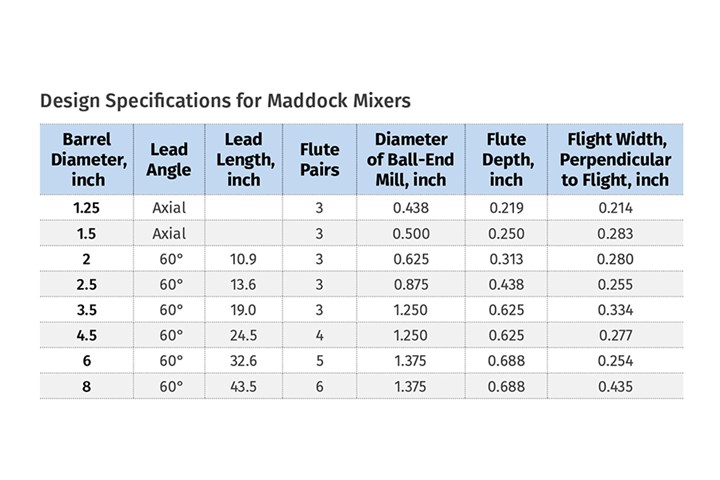
Maddock mixers are the preferred dispersive mixer for single-screw extruders. Its design is critical to the elimination of solid polymer fragments and entangled PE gels. Moreover, flute design is important to mitigate resin degradation.